Based on standard delivery, ex. VAT
How to select a Heat Recovery System
Industrial / Commercial
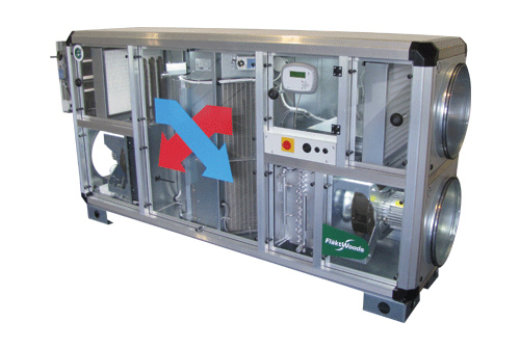
Why use a heat recovery system?
- “Nearly half of the UK’s co2 emissions come from buildings, and half of heating/cooling cost is caused by ventilation when it is done by the “open window” method according to the regulations”.
- Correctly selecting ventilation recovery units in a building can be the most cost-efficient, sustainable and quickest way to reduce buildings energy consumption. An added benefit is this can also provide better indoor air quality (IAQ) and protect buildings from (Sick Building Syndrome SBS).
Not sure if it applies to my circumstances?
-
The ‘air tightness’ of a building is increasingly being targeted to improve building efficiencies and reduce energy bills, meaning (in most cases) for newer buildings, there is a greater need for ventilation by heat recovery. This helps to reduce running costs and building owner and occupiers can save more money over a period of time.
What Industrial / Commercial buildings should I use Heat Recovery?
Heat recovery can potentially be applied to any HVAC system that uses duct work to supply and extract ventilation air. You can commonly find opportunities in:
- schools
- offices
- lecture theatres
- hospital wards
- swimming pool halls
- manufacturing areas
It’s worth noting that installations in new buildings where mechanical ventilation is being provided are almost certain to contain some form of heat recovery. This is because current building regulations demand a level of efficiency which is very difficult to achieve without it and such techniques are now commonly adopted.
There are so many options on the market, what’s the minimum I should include in my Heat Recovery Unit?
- 100% Bypass — To get the most from your Heat Recovery Unit 100% Bypass is a must have, when used in conjunction with the minimum controls below, your Heat Recovery Unit will give you the most optimum efficiency. 100% Bypass prevents you from recovering heat during the summer months when you want to get rid of heat within the building. Bypass also gives you an option to have free cooling in summer* with a controlled balance of fresh air and recirculated heat
- Re-Heat Devices (the two most common types of heating devices are Electric and LPHW (water) coils) — Re Heat is another must. Re Heat will add extra heat to the recovered air when needed, no Heat Recovery Unit can be 100% efficient no matter what you read, meaning the recovered heat will never reach the temperature of the ambient air in the building, why is this a problem? As a quick example when the outside air temperature is ‑4C and the inside ambient is 22C the recovered heat air temperature will be approx (depending on RH levels) 11C after the heat exchanger if this air is not then reheated (topped up) you could end up reducing the overall building temperature and increasing the load on the main heat source. If this air is reheated to 22C no overall temperature is reduced and no additional requirement is put on the main heating source.
- Controls — to control the incoming, return and supply air a number of temperature sensors are required to be mounted within the unit. To enable full optimization of these temperature sensors fully integrated controls will be required to realize the full potential of your Heat Recovery Unit.
- Temperature Sensor (preferably a duct sensor) — To get the most from your Heat Recovery Unit, this sensor is used to ensure the unit is balanced to supply air at the optimum required temperature within the room, we would suggest this will change between summer conditions and winter conditions, just like your central heating thermostat at home. In winter you want to ensure the return air is warm enough not to feel a cold draught. In summer you want to ensure you make the most of free cooling to make those long summer days and nights as comfortable as possible*
- Passive Infrared Sensor — used to detect occupancy
- CO2 Sensor — Have you ever felt tired in class in the afternoon, one of the main reasons is a high level of CO2, and poor indoor air quality (IQA), and this sensor will increase the ventilation rate on demand. Thus keeping co2 levels at a normal level which will increase productivity in the work place.
- Humidity Sensor — Modern buildings are becoming air tight which seals off the movement of moisture, this has resulted in a secondary problem of condensation forming in and around walls, which encourages the development of mold and mildew. Good ventilation can be used to remove this stale, moist air and replace it with clean fresh air.
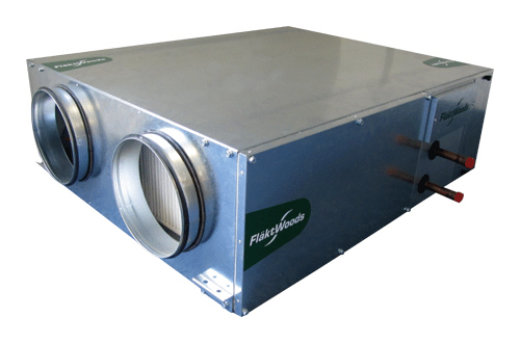
I need more convincing Heat Recovery is the right choice for me?
Energy Recovery Comparisons based on an independent study based on one Heat Recovery Unit (Supply and Extract)
Energy Consumption (kWh)
- 10,267 kWh None Heat Recovery
- 3,011 kWh with Heat Recovery
Carbon Usage / Saving (Tons)
- 5.3 tons of co2 None Heat Recovery
- 1.8 tons of co2 with Heat Recovery
Running Costs / Savings (UK Pounds), Based on a correctly sized Flakt Woods ECO STAR Heat Recovery Unit
- £1602 None Heat Recovery
- £470 with Heat Recovery
Payback
- 2.7 years based on a correctly sized Flakt Woods ECO STAR Heat Recovery Unit
* Free cooling is when the external air temperature is below the internal ambient air temperature and the internal ambient air temperature is higher than the temperature sensor setting. In this instance the heat exchanger will be in 100% bypass and full fresh air will be delivered via the supply system and help to reduce the internal ambient air temperature thus giving free cooling
Example - External air temperature 20C, internal ambient air temperature 30C, temperature sensor setting 24C, free cooling will occur.
Follows a more in depth look at Heat Recovery
What is a Heat Recovery System?
Heat Recovery Systems are used to introduce fresh air and remove warm stale air from buildings. They work by recovering the heat from the stale, warm air and transferring it into the incoming fresh air using a plate heat exchanger. This eliminates the need to have to re-heat the space that the stale air was taken from.
Figure 1 — Typical Plate Heat Exchanger Principle
Figure 2 — Typical Plate Heat Exchanger
Why is a Plate Heat Exchanger Used?
A plate heat exchanger is typically comprised of a series of parallel aluminum plates, which direct the intake (supply) air and exhaust (return) air, see Figure 1 and 2. The supply and extract air streams cross over each other, but are separated by the parallel plates, which allow heat energy to be transferred from the exhaust air to the incoming air supply via conductivity. It recovers energy from extracted air that would otherwise be lost to the atmosphere and uses it to pre-heat the incoming fresh air.
The material, thickness, surface area and air volume affects the efficiency of a plate heat exchanger, which typically will provide efficiencies of between 50% and 60%. New technologies such as counter flow heat exchangers efficiencies can increase up to 95%.
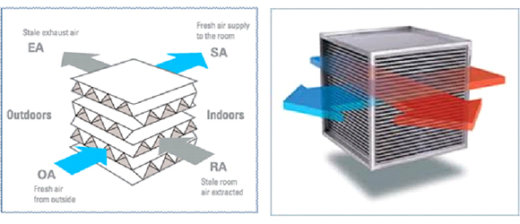
Below demonstrates the principle and structure of the heat exchanger type. The use of a plate heat exchanger reduces the amount of energy needed to heat (or cool) the supply air to the required temperature.
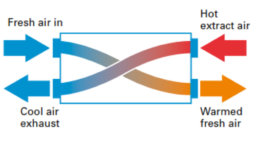
Why is Heat Recovery Ventilation (HRV) required in buildings?
The ‘air tightness’ of building is increasingly being targeted to improve building efficiencies and reduce energy bills.
This has resulted in ventilation systems being required to deliver more fresh air than before, usually to a greater occupancy and internal comfort level whilst ensuring that energy is not being wasted and indoor air quality is at the correct levels.
In modern buildings you need to balance the requirements for ventilation systems to provide sufficient fresh air with efficient energy consumption. Heat recovery through the ventilation system, which would otherwise be lost, can reduce energy consumption in your building.
Where can Energy Recovery be applied?
There are many applications of heat recovery technology in ventilating and air-conditioning systems, but they are based on a few simple techniques.
Heat recovery can potentially be applied to any HVAC system that uses ductwork to supply and extract ventilation air. You can commonly find opportunities in
- school
- offices
- lecture theatre
- hospital wards
- swimming pool halls
- manufacturing areas
It’s worth noting that installations in new buildings where mechanical ventilation is being provided are almost certain to contain some form of heat recovery. This is because current building regulations demand a level of efficiency which is very difficult to achieve without it and such techniques are now commonly adopted.
Example using typical UK Conditions
External Design Temperatures (Based on CIBSE Guide B for the area of MANCHESTER)
Winter Design Temperature: ‑4 ° C db 90% RH (max)
Internal Design Temperatures (Based on CIBSE Guide B table 1.1)
Winter Design Temperature: 21°C db ± 2°C & 30% RH (min), 55% RH (max)
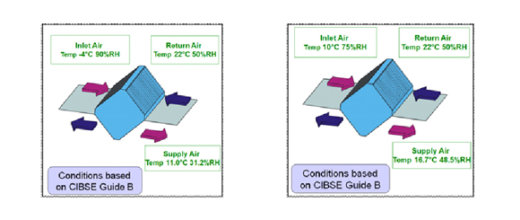
Figure 1 based on ‑4 °C Inlet Air Figure 2 based on 10 °C Inlet Air
This means in terms of energy saving for a typical winter’s day, instead of heating fresh air from ‑4°C to a room condition of 22°C, your incoming air is now tempered by using the extract air over a plate heat exchanger to 11°C. This significantly reduces your heating running costs while providing clean fresh air into the space.
How to select an Energy Recovery Unit
Example for a typical school
In terms of the design and calculations there are two design scenarios:
1. A fully mechanical ventilation design that will not require any additional openings such as windows or louvres for fresh air purposes.
2. A mixed mode ventilation design whereby the mechanical ventilation system will provide enough ventilation most of the time, however additional openings will be required for purge ventilation only.
For the purpose of this design calculation a fully mechanical ventilation design will be considered.
The main design guides for this development will include, but are not limited to:
- Approved Document Part L2A 2010
- CIBSE Guide B
- Non Domestic Building Services Compliance Guide 2010
- Building Bulletin 101 – Ventilation of School Buildings (2006)
First you need to determine the amount of supply and extract air required to serve your area to meet design criteria and requirements.
To do this you need to know your design occupancy, a typical UK classroom would be 32 persons.
For a typical classroom under BB101 requirements, a minimum ventilation rate of between 3l/s and 8l/s per occupant is required.
In this example the amount of air that should be supplied to the classroom is:
- 32 (the number of persons in each classroom)
- x 8l/s (maximum ventilation rate per person)
- = 256l/s per classroom
So in this example the supply fan required within the energy recovery unit (ERU) for a single classroom with 32 children is:
- 256l/s (litres a second)
Most ERU publish the unit performance in m3/hr or litres / second (l/s). A separate ductwork pressure drop will required to be undertaken to determine the pressure drop of the system.
Due to the need to recover the exhaust air energy and pre-heat the incoming supply air, the ductwork associated with the various air paths must be coordinated within one area. Allowances must be made for routing of the ductwork through the building as four different air paths must be coordinated within one area.
Typically for a locally mounted unit serving a single classroom, 150Pa would be sufficient, however we recommend a pressure drop calculation for your system is carried out.
PLEASE NOTE: As the plate heat exchanger must be installed within the ERU, access for maintenance is also required, adding to the overall plant space required.
If you use our fan selection tool a list of fans suitable for your building the only things left to consider are:
- Noise
- Specific Fan Power and Part L
- Efficiency
- Controls e.g. Controls, Co2 sensors, Humidity Sensor, Passive Infra-red (PIR) Sensor
- Re-heaters and by-pass
- Environment
- Price, Quality and Brand
We assume this is what the majority of people usually consider – with efficiency being the biggest driver, we would recommend you should consider the following
- Noise – No one wants to be working in a classroom with a noisy fan running overhead, BB101 recommends a unit with a casing radiated (Breakout) noise level no higher than 30dB(A) at 3 meters from the listener to maintain comfort.
- Specific Fan Power – Approved Documents L2A and L2B come into force on 1 October 2010. The guide provides detailed guidance for fixed building services in new and existing non-domestic buildings. It covers work on both new and replacement systems, identifying the differing requirements where they exist. The guide outlines requirements for compliance, key terms, standards, and efficiency calculations. In addition the guide highlights publications that include information on good practice for design and installation over and above the recommended minimum standards outlined. To install a zonal supply and extract ventilation units such as ceiling void or roof units serving a single room or zone with heating and heat recovery in to an existing building the maximum permitted Specific fan Power (max) is 2.0 W/(l/s). This means more units will use EC motor technology to deliver reduced energy consumption.
- Efficiency – your always find a unit to suit your design requirements – The initial capital is only 10% of the total cost to the end user. We have to pay more attention to the energy efficiency (and hence usage) than to the investment cost only, which traditionally is the case.
- Controls – As standard, all e3co Star models are fitted with pre-set controls, this allows service engineers to quickly configure air flow modulation and optimize energy usage. It also has intelligent energy saving functions built-in, including night cooling, frost protection, temperature control and low temperature defrost. Plus, to simplify building integration, controls have full BMS capability, via an open table Modbus BMS protocol.
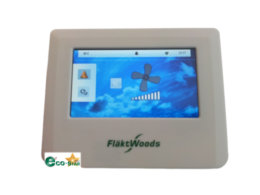
- Re-heaters — The e3co Star range is available in three variants. The entry level e3ssential is supplied with factory fitted plate heat exchanger and filters, while the e3nhanced additionally incorporates a water or electric post heater. Finally the e3lite adds an electric pre-heater. All models have an integrated bypass damper, providing a 100% heat exchanger bypass capability.
- Environment – Legislation requirements for fans (such as Part F and Part L) now mean in new buildings where mechanical ventilation is being provided are almost certain to contain some form of heat recovery. This is because current building regulations demand a level of efficiency which is very difficult to achieve without it and such techniques are now commonly adopted.
- Price, Quality and Brand – remember most of the time you get what you pay for.